The first years of this decade have been marked by volatility in the wake of the global pandemic. There is significant global uncertainty and unrest, caused by factors ranging from extreme weather events, supply chain disruption and conflict. According to the World Economic Forum’s Global Risk Perception Survey 2023, 80% of respondents anticipated consistent volatility over the next two years. Failure to mitigate climate change over the next ten years, was seen as the biggest risk by the majority of respondents. For businesses in any sector the challenges arising are destabilising.
For medical technology (MedTech) companies, these challenges are compounded by the continued acceleration of technology disruption. MedTech companies must find a way to meet global demand, continue to drive innovation and productivity while also remaining agile, resilient and increasingly importantly, sustainable in a world of volatility, uncertainty, complexity, and ambiguity (VUCA).
It is estimated that 133,000 skilled scientific and technical workers will be needed across the next decade, 90,000 of which will be in MedTech, particularly R&D and manufacturing. At the same time companies are striving to meet Industry 4 and 5 standards, which increases the use of new technologies and in turn creates greater demand for new digital skills.
Collaboration across industry sectors such as technology, medical technologies, biopharma and engineering are a critical part of helping to deliver next generation medical solutions. Manufacturers of the future will need skilled workforces and a strong infrastructure that gives them access to talent, research resources and partnerships and collaborations that can leverage global reach while also providing local support in areas such as addressing regulatory requirements.
MedTech companies must also transform their manufacturing and supply chains through digitalisation. This is key to ensuring more efficient, faster operations which can also drive innovation through data collection and predictive analytics. Data, Machine Learning and AI are integral to digitalisation as they can predict demand but also provide an overview of the value chain. This is critical to the smooth flow of a product, right from the research and development phase, through to production of prototypes and eventually delivery of products.
Leaning into support for business must also be a top priority. Investment in research and innovation remains key to meet increased demand for existing and future medical technologies. This requires a supportive ecosystem. In Ireland, where 14 of the world’s largest 15 MedTech companies have operations, the fact that 75% of global MedTech companies with operations in Ireland are carrying out R&D speaks for itself.
New product innovation is critical to success and growth, but funding R&D can often be a barrier to investing in innovation. This report highlights how companies have found benefits in growing their business in Ireland, which offers R&D and innovation funding and collaboration opportunities through organisations, infrastructure and supports such as Science Foundation Ireland, technology centres and gateways, R&D grants and attractive R&D tax credits. Partnerships between industry and research centres can bring major advances in technology, reducing the financial burden and risk to companies.
This report also outlines how Irish-based MedTech companies are addressing these challenges against an unprecedented period of global competition, competitiveness challenges and business model change.
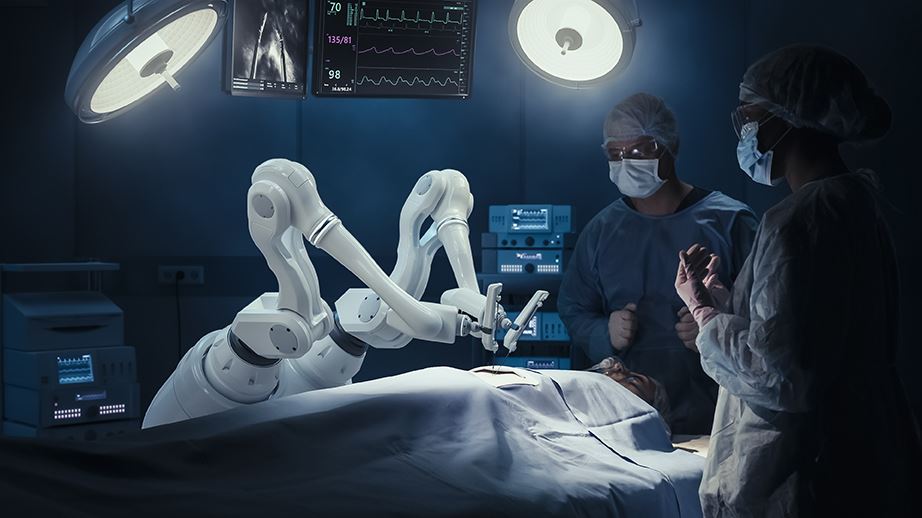
Section 1 – Tapping into a strong, connected ecosystem
A reliable supply chain is crucial for successfully launching and getting MedTech products to market. The pandemic highlighted the need for resilience and adaptability as global supply chains closed, opened, slowed down and ramped up at different times around the world. Increased forecast variability and disruption to distribution centres, transport logistics, and manufacturing sites have a knock-on effect over the whole supply chain. Successful companies needed to be able to respond to shifting demand patterns and global supply disruption and reconfiguration whilst managing sustained demand for new products.In a fast-moving situation it is essential to have detailed insight into how production lines are performing to identify and resolve issues in real-time. Shane Maher is Director of Production Planning and Logistics Joints Reconstruction & CMW at DePuy Synthes, a J&J company and designated a World Economic Forum ‘lighthouse’ for Industry 4.0 and digitalisation. The based Cork site manufactures hips and knees, shoulders and power tool products to the medical device market. Shane says: “We’re rolling up our digital approach in such a way that people in the organisation can make the best decisions by making sure they have enough information in front of them at the right time. For example, decisions based on competing demand within a constrained supply situation – prioritising and deciding which product we make.”
The supply chain challenge facing MedTech companies is neatly summarised by Mark Hennessy, Executive Director of Manufacturing at Bausch and Lomb, in Waterford. He believes supply chains are quickly impacted by external issues with raw materials and logistics and transportation. “We try to mitigate some of this by looking at simplifying our processes and our supply chains. Previously we might have had a three-month stock of a particular raw material to protect against any fluctuations. Nowadays it is more typical to hold six or nine months on key materials or components because of that global uncertainty with respect to supply from vendors,” he says.
Seamus Maughan is Manager of Global Supply Chain at Baxter Healthcare in Mayo, which provides a broad portfolio of essential renal and hospital products. He says: “Automation has enabled us to successfully implement capacity projects. Baxter had a shortage in the US a number of years ago due to a hurricane. We took over and through the use of automation, we were able to get product to them straight away through our ability to ramp up rapidly. We can successfully deliver big projects, with the correct technical solution and on time with a good use of capital. We have a good technical base here in the country, working with a host of automation companies.”
According to Digital Manufacturing Ireland (DMI), a newly established national centre launched by the Irish Government to assist manufacturers in rapidly adopting digital technologies, supply chains are undergoing a transformation into ‘intricate and delicate systems’, grappling with increased complexity. The challenges, heightened by the aftermath of the pandemic, are compelling manufacturing organisations to confront rising shortages and disruptions in their supply chains.
Claude Costelloe, Director of Manufacturing Operations and Supply Chain at Digital Manufacturing Ireland, notes, "In response to these shifts, manufacturing entities are actively working to bolster the resilience of their supply chains. This strategic approach often involves maintaining higher inventory levels, optimising supplier networks, and, in some cases, seeking local suppliers. However, such measures can incur additional costs."
Traditionally, supply chains operated within silos, featuring non-real-time information flow in one direction. The contemporary landscape demands a more resilient approach, prompting organisations to digitalise their supply chains. This transformation entails establishing an end-to-end connected supply chain where information flows bidirectionally in real-time. The goal is to enable dynamic and predictive responses to challenges, allowing manufacturers to react promptly to outages, shifts in demand, and evolving customer priorities.
Claude Costelloe cites Digital Manufacturing Ireland’s facility in Limerick as an example of a fully connected, representative digital manufacturing line that exemplifies the potential of an end-to-end supply chain. Leveraging various technologies and capabilities, DMI clients can embark on their digital journey with industry-led technical support.
Notably, the successful digitalisation of supply chains hinges on developing new roles and skills. A global survey within high-end manufacturing organisations disclosed that a significant portion of current supply chain roles would undergo transformation in the next three to five years. While 66% of respondents recognised upskilling as a priority, a mere 7% indicated that their organisations prioritised this crucial enabler.
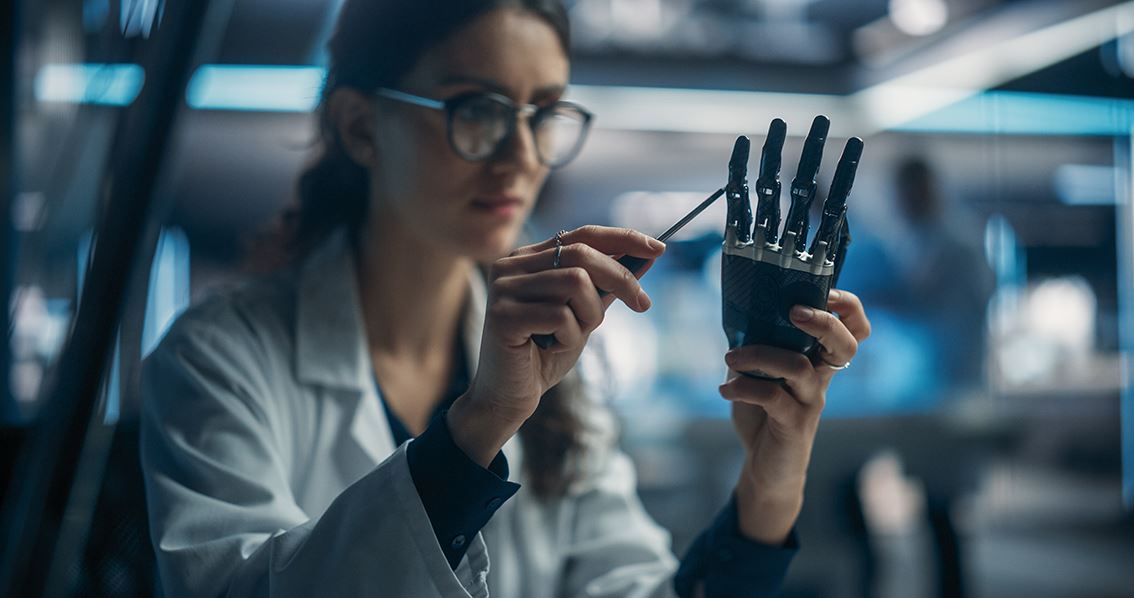
Talent and resource flexibility
James Jordan is Head of Operations at Baxter. He says: “In today's world, we’ve had to be very inventive and work well with the team here to be able to ramp our manpower as required. It’s about being ready to step in and create some capacity so that we can put our hand up and take business in when the business needs it.“To flex demand in this way, it is necessary to be able to quickly access people with the right skills. We are part of a global hub here in Castlebar, where expertise is grown both through academia and well-established companies growing their own talent, funded internally and/or with the support of Government.”
Mark Hennessy says: “That's one of the huge advantages with Ireland where, when you hire staff, they usually have had a lot of experience and hit the ground running. A high degree of talent and leadership comes out of the Irish operations.”
Cross-sectoral talent and good cooperation between national and local level business and MedTech are also advantages to help drive improvement. Mark says: “The ecosystem in Ireland is a distinct advantage to us when compared to locations around the world that don't necessarily have that close collaboration or that network that they can rely on. In Ireland companies are always looking at different and better ways to do things and you can see what other companies are doing that’s having a positive impact on their operations.”
Good support networks and the ability to continue to scale up at pace despite so many external challenges to the supply chain makes Ireland an attractive place to continue to do business. Mark says: “Ireland is still a very attractive place for new investment because we’re efficient and we deliver.”
According to Domhnall Carroll, CEO of Digital Manufacturing Ireland, there is significant potential in fostering collaboration among firms. He says: “Since its launch in early 2023, DMI has observed a growing demand for swift and profound collaboration within the ecosystem. In response, we are establishing Centres of Excellence aimed at expediting the widespread adoption of transformative technologies and practices within manufacturing sites.”
One notable initiative is the Visual Cognitive Manufacturing Group (VCMG), where sixty organisations have united to promote the extensive implementation of vision technology. Domhnall Carroll explains that the VCMG has identified twelve challenge areas, and cross-industry teams are currently collaborating on developing solutions. “The synergy between manufacturing companies, technology firms, academia and the DMI team ensures that all the necessary components for a successful outcome are readily available, fostering a cohesive and effective collaborative environment,” he adds.
Regulatory affairs and a supportive ecosystem
MedTech is a highly regulated industry that has seen unprecedented change in recent years. As evidenced by the EU Medical Devices Regulation and In Vitro Diagnostics Medical Devices Regulation, the regulatory environment is evolving to ensure the continued safe and effective development of new medical devices and diagnostics in the face of rising demand. A strong regulatory function is therefore central to the success of any MedTech operation.Having a regulatory function involved at forefront of the innovation process can ensure regulatory considerations can be assessed and planned for at the outset. Emmett Devereux is Director of Government and Regulatory Affairs, EMEA for Cook Medical. Headquartered in Bloomington, Indiana in the United States, Cook has a base in Limerick, and is one of the longest established companies in the mid-west MedTech community.
Emmett explains that his role in this is to engage as many people as he can from regulators to stakeholders, understanding key considerations and impact to the patient and product of regulatory changes. “For products already on the market, you need to make sure that there's no ambiguity with the regulations” he says. “You must fully understand the current requirements from a product portfolio perspective, where it's going and what is going on in the market. To do that you have got to be involved globally with numerous groups and get a clear understanding for what is coming down the line.”
Emmett believes that Ireland has a great deal to offer with a well-developed MedTech sector. “From research to distribution and everything in between, you get the complete product lifecycle, and how that relates to any forthcoming regulatory changes. Our site in Ireland and our Cook sister sites can see the end-to-end global picture because we ship to over 137 countries across the globe.”
He adds that the regulatory role is the lynchpin between all company functions, stakeholders and regulators, communicating between all sides and building trusted relationships.
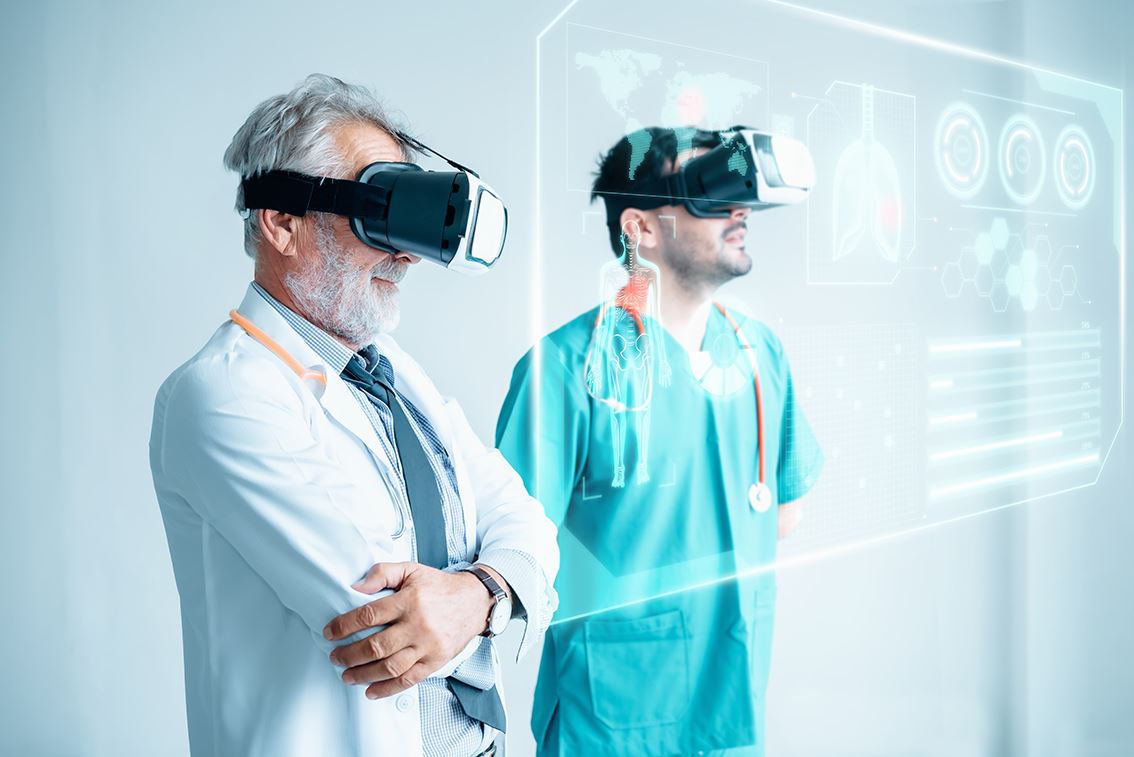
Section 2 - Transforming manufacturing and supply chains
Despite challenges when it comes to transforming manufacturing and supply chains, there are significant opportunities around digital and disruptive technologies from an advanced manufacturing perspective.Recognising the potential around Industry 4.0 and 5.0, forward-looking MedTech companies are shifting to highly advanced/smart digitalised lines, integrating cutting-edge software with advanced technologies such as robotics, automation and AI to drive efficiency, productivity, quality and operational excellence. ‘Lighthouse’ factories are showcasing how the industry can address complex challenges; strengthen supply systems and introduce digital technologies that enable them to transform operations and drive competitiveness.
Janssen Sciences Ireland (a J&J company) has a Global Centre of Excellence for Clinical Drug Substance and Drug Product Release and Stability Management. Based in Cork, its manufacturing and operational excellence has also been recognised as an ‘Industry 4.0 Lighthouse’ by the World Economic Forum. Recognising that customer needs were changing and that production data was becoming just as important as the product, a test and learn strategy was used across different sites throughout the business, to see how digital and tech could add value across the supply chain.
Gary Hartnett is President of Partnership and External Supply, Janssen Global Supply Chain and former Site Lead at Janssen Sciences Ireland. He says: “We started off with Industry 4.0, merging between digital and tech, looking across lots of different elements such as the cloud, big data, Internet of Things and cyber security. We also looked at ways to duplicate from one machine to another, robotic arms, cyber security, data analytics and so on.
“With a number of sites all working differently and providing different feedback, we started to put a structure and a framework in place here in Cork, which began to increase competencies and capabilities.”
However, not all companies have the capability and resources to make this strategic change. Research from the World Economic Forum has found that around 70% of companies investing in technologies, including big data analytics and AI, fail to implement their strategies and projects do not go beyond the pilot phase.
Domhnall Carroll underlines DMI's industry-led ethos, focusing on strategy, technology, and people as the key elements for successful technology adoption and digital transformation. He says: “Our facility in the National Technology Park, Limerick, is ideally located to support companies across Ireland and beyond, as we develop our supports for technology, operations, and the workforce of the future.”
Mike Kiely, DMI’s Senior Manager, Data Science and Digital Twin, explains: “Our role is to provide exposure to the most suitable technology to fulfil a need for our clients. Using our experience, we can help integrate these solutions within the existing technology ecosystem of the enterprise.” Kiely highlights that this approach not only accelerates the adoption of cutting-edge digital tools, but also creates an environment where companies can thrive in an increasingly competitive and technology-oriented market.
Addressing a key driver for manufacturing enterprises, Kiely says: “One challenge for all manufacturing enterprises is 'How to become a Data-Driven Organisation.' Within DMI, we support companies by benchmarking their current state with industry best practice. From there, they can identify data-driven insights and decision-making opportunities to make that important transition.”
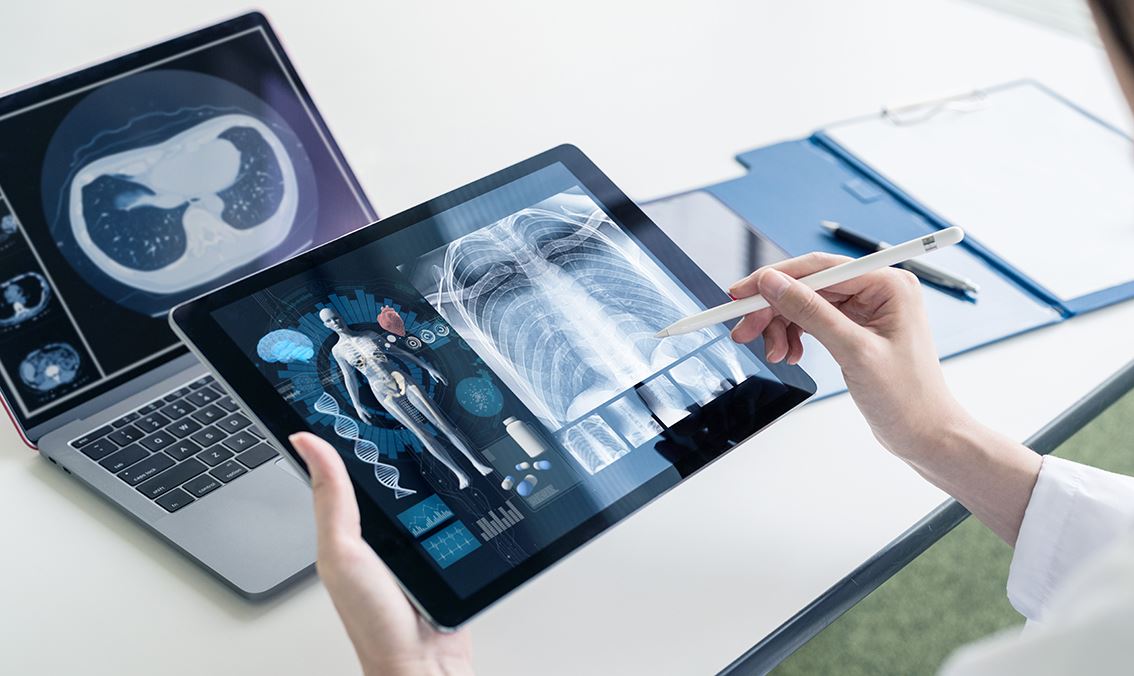
A roadmap that evolves with digitalization and innovation
Even for those already on the digitalisation journey, the rapid evolution of technology is posing challenges. Transformation roadmaps that began within the last two decades initially focused largely on data collection.DePuy Synthes Cork’s digitalisation journey began in 2002 with an initial focus on using data to control the supply chain in terms of managing logistics of product supply, as well as global markets and management of the regulatory side of the business. When the business expanded, there was a need to accelerate product launch, which shifted the focus to innovation and technology. The launch of DePuy’s Innovation Centre in 2018 changed the site’s direction from manufacturing and logistics management, to being more technology oriented, incorporating packaging development systems, machine tech development, automation and digitalisation.
Colm Hynes, Global Supply Chain, DePuy Synthes, says: “We started to go down the automation route, but with a digital perspective - a data focus rather than just automation for automation’s sake. We saw the need to automate but in parallel we put in the digitalisation layer.”
Around the same time, an increase in market complexity and the regulatory environment created a paper-based organisation where spreadsheets, data and interfaces between the ERP system and all other systems across the company were being managed manually. A new system was needed to remove the manual layer.
Colm says: “We had one set of people in the Innovation Centre looking at analytics from existing business and another set of people from the global supply chain looking at the analytics of all the data that was coming from the markets. These two parts of our business have now come together and became very much focussed on data management and that's where it has evolved today.”
At Janssen there is a 2030 vision to build a digital and tech hub which will provide the next global business service. Value measures around speed to market, cost and sustainability have helped to create a digital roadmap for 2030. Each site has different levels of modelling for different technology platforms such as vaccines or large molecules and each site has its own digital roadmap.
Gary Hartnett says: “Seven programmes run underneath that system: Digital performance management, smart asset maintenance, digital worker, supply chain analytics, integrated data management, smart tech transfer, real time-release integrated quality.”
Data is used differently at each site. For example, where a site that is involved in new molecule development it will collect data from that molecule, tracking the biology and digital imprint to help take that molecule through all the development phases more quickly and reducing the risk of failure at early-stage modelling.
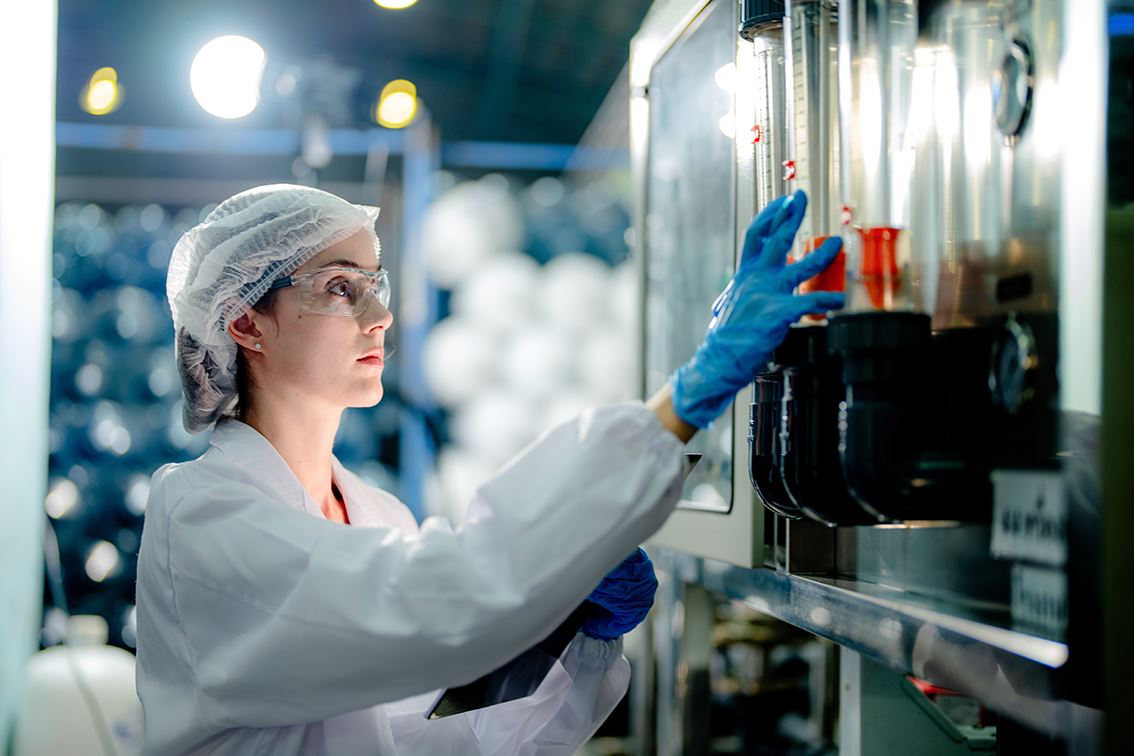
Automation and AI
An increase in automation is key to enabling the quick and safe scaling of production. The use of AI is now helping to create extra capacity through automating labour-intensive manufacturing processes such as inspection.At Boston Scientific, which has three facilities across Ireland manufacturing complex medical devices such as coronary coils, ICD and catheters, the digitalisation process has been underway for 18 years. As technology develops, the focus has moved away from more traditional manufacturing that focuses on hardware, to building databases and systems for taking data from systems, analysing, predicting, and being able to share data extensively across its engineering organisations. Automation has become a priority to make vital quality assurance checks which can sometimes incorporate the need to manually check for 40 or 50 different defect types.
Michael Murphy is Director of Facilities, EHS and Equipment Engineering at Boston Scientific’s Galway site. He says: “The journey now is to try and make effective use of AI and virtual reality (VR) to drive innovation, improve efficiency, enhance user experiences, and gain a competitive edge in the MedTech sector. With product quality and patient care at the heart of the MedTech sector mission, digital inspection applications using AI algorithms will be a potential game changer to the industry”.
DMI is strategically leveraging the rapid advancements in AI through its Visual Cognitive Manufacturing Group (VCMG). This Centre of Excellence (CoE) enables manufacturing companies to gain access to cutting-edge AI technologies, particularly in machine vision. This collaboration will aid the rapid adoption and integration of these technologies into manufacturing company’s production processes.
Currently there are approximately 60 manufacturing companies within this CoE. This indicates the demand from industry towards the adoption of AI for vision. “The participating companies come from a range of industry sectors, and they also come from a range of maturity regarding their adoption of machine vision. DMI will be the hub for this innovation and ultimate adoption of these technologies on the factory floor,” says Mike Kiely from DMI.
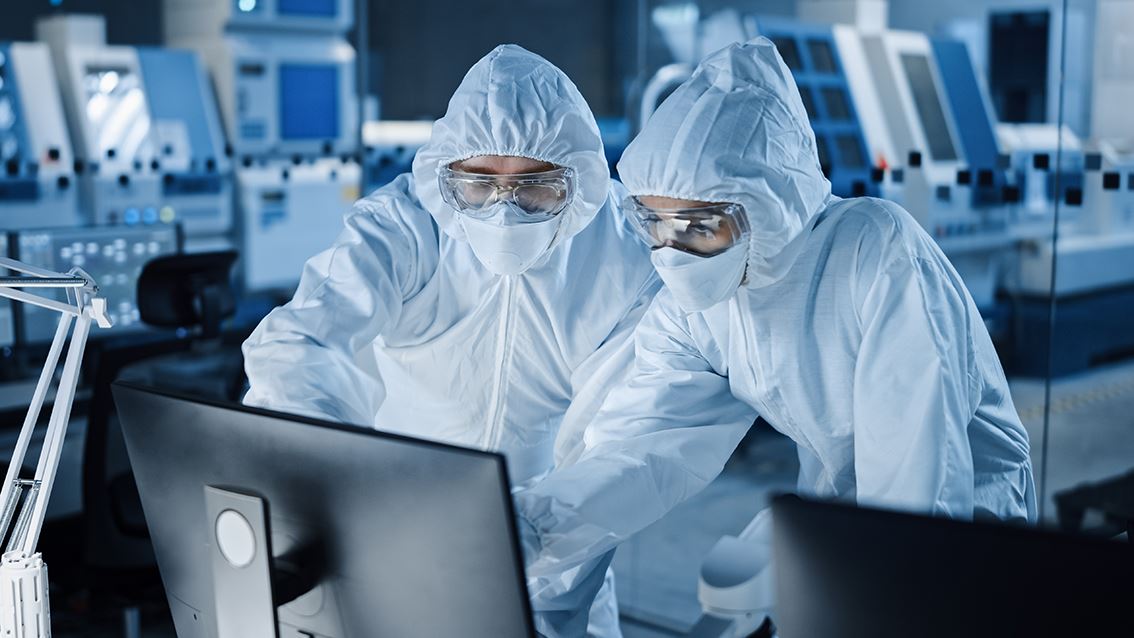
Use of data analytics
The use of data analytics is critical to being able to understand, predict and respond to market need in real time, while also providing greater visibility of trends and changes across global supply chains. Connected factories are enabling businesses to integrate IT systems across the whole organisation, moving away from departments working in siloes and ensuring that data is turned into intelligent information that can help to drive actionable insights and continuous improvement. It can predict when and where things might go wrong, enabling preventative action to take place. It also enables greater standardisation particularly in larger organisations.At Boston Scientific, business analytics drives standardisation across the manufacturing network. Michael Murphy says: “As a company data analytics plays a crucial role by providing valuable insights from vast amounts of data we generate and collect. The strategic benefit of data analytics provides us with insights that improves decision making and optimises value for our customers.”
For DePuy Synthes, one of the strongest developments has been the digital performance dashboard, allowing for enhanced and centralised plant management. Live data streams from across the business pool data into a system which highlights key performance metrics, including information from quality management systems. Data is extracted from the ERP system, time and attendance system and the training system to give an overall picture of activity on site at any time.
Colm Hynes says: “This has been groundbreaking from a J&J perspective. The original idea was a manual process, but we completely automated and digitalised it. The automation team that we set here, and the digital and analytics team that were part of that have now been ‘lifted and shifted’ into a global organisation.
“The speed of decision-making is significantly higher than it would have been before, simply because we are pulling the data that drives the system into our dashboards and are able to highlight with various algorithms exactly where we have a problem.”
The system highlights where stock can be reallocated to markets where there is greater need and demand. Colm adds: “I would say without a doubt, that the greatest value in digitalisation sits in effective supply chain management.”
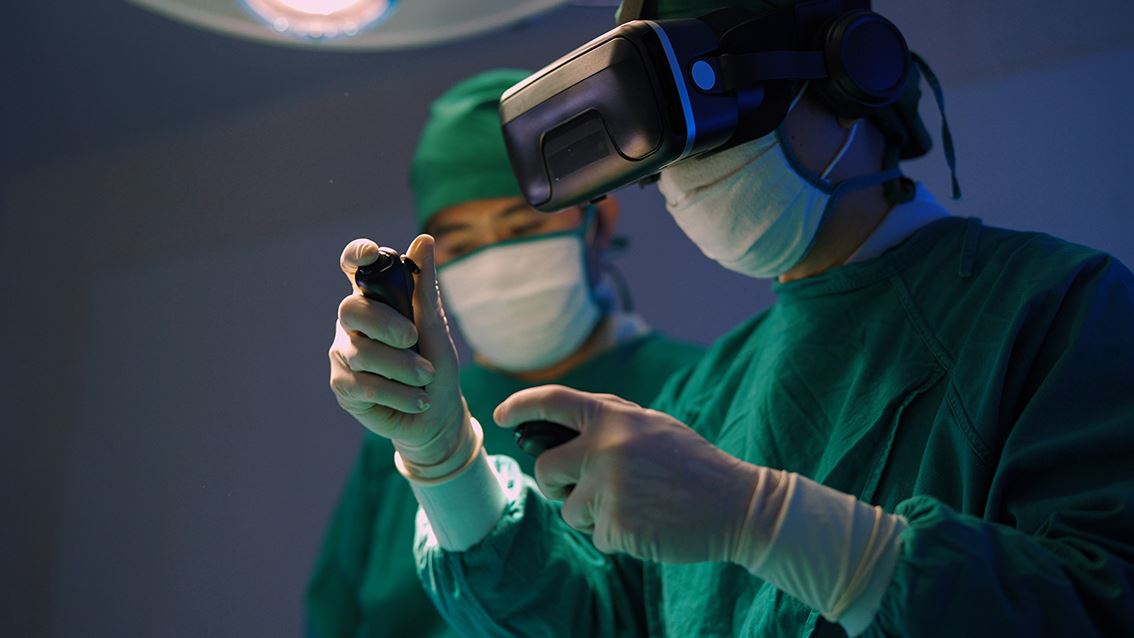
Resource and capability
As new technologies develop, so does the need for the right talent to drive innovation. Companies need to be sure of what expertise they need and have good networks to help develop that. Creating partnerships with academic networks can help to grow the new talent needed, but equally important is engaging with the current workforce to use their insight to help drive change throughout the organisation.A good example can be seen at DePuy Synthes, where a new department has been set up to focus on digitalisation. This department was responsible for digital twinning, a concept that contributed to the site being designated as a WEF Lighthouse site.
Modelling equipment and designing it in the virtual world enables project teams to spot the need for modifications before it is put together. During the global pandemic, this was particularly effective in enabling Factory Acceptance Tests, where in normal circumstances, visits would be made to manufacturing sites to view and verify the build of the equipment. Instead, this could be done using Google Glass and virtual or augmented reality. The team has also recently created its first AI bot that aggregates key data and automates the decision to send purchase orders automatically into the supply base.
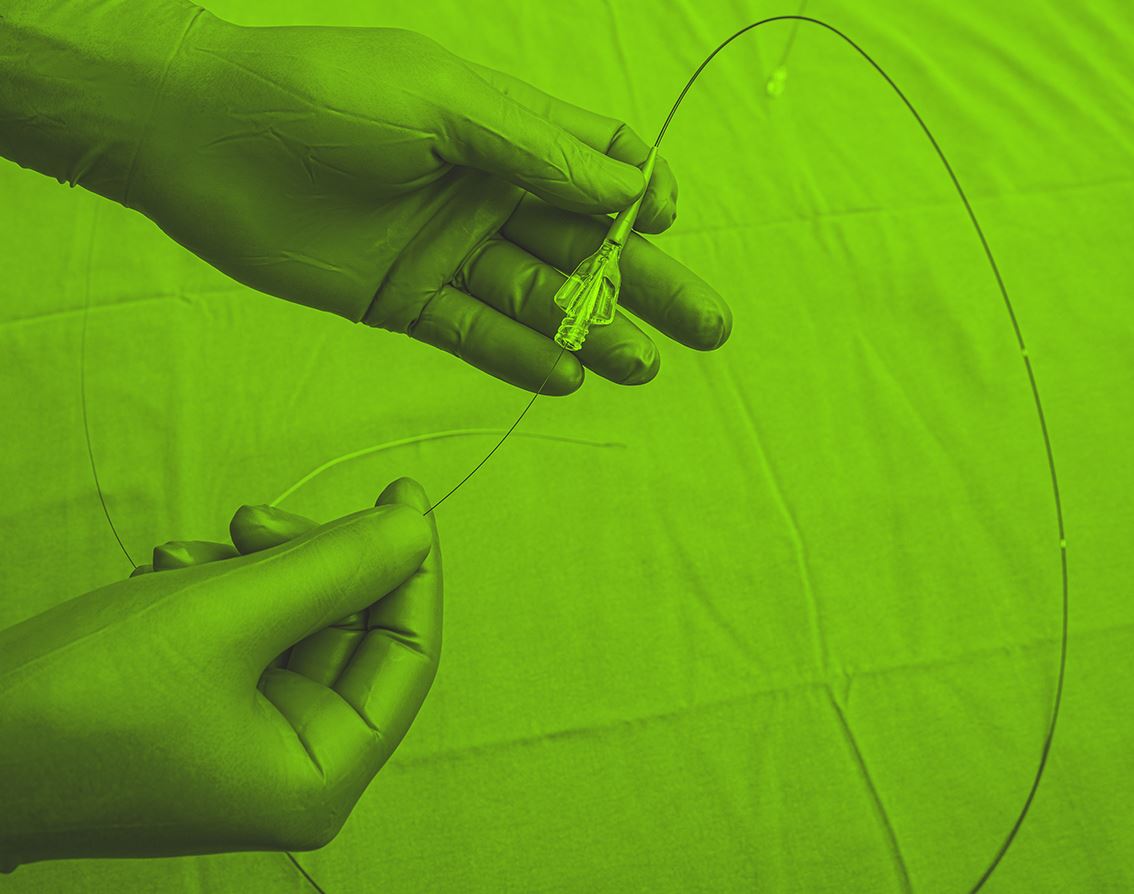
Section 3 - Leaning into support for business through R&D, skills and sustainability
Research and development around medical technologies was thrown further into the spotlight during the pandemic with the need to quickly develop diagnostic tests, administer vaccines and develop novel ways of treating and supporting COVID-19 patients.
Breaking new ground is always risky and collaboration through academic and commercial partnerships is often key to successful new product development. Research is typically funded by a company itself, which can be a significant investment in the case of earlier stage research. Having access to research and innovation supports also help mitigate those risks and support the innovations of the future.
To remain competitive and meet customer demand rapidly, companies benefit greatly from having access to an ecosystem that enables them to ramp up activity and collaborate in order to drive innovation. Gaining access to materials and prototypes can take several weeks or months, so building good relationships with the right suppliers and partners is fundamental.
Michael Gilvarry, General Manager with responsibility for research and development at CERENOVUS agrees. The company’s Galway site develops advanced devices that remove blood clots from stroke patients in the critical hours after stroke has occurred. He says: “From a research and development perspective, we’re very focused on developing new minimally invasive products so we put a lot of work into understanding what clinical challenges can present themselves, researching and simulating those needs and then innovating to address those real-world situations. We then need to be able to quickly develop physical prototypes so that we can start moving quickly.”
CERENOVUS has benefitted from the Irish ecosystem to help drive innovation through a partnership with Medical and Engineering Technologies Gateway (MET), part of the Atlantic Technological University (ATU). CERENOVUS worked with the centre to establish several programmes, one of which included a PhD programme focusing on the characterisation of thrombi in acute ischaemic stroke after it developed an innovative clot-retrieving device designed to treat patients with the condition. Funding was secured from the Irish Research Council (IRC) to help develop the research.
Michael Gilvarry says: “From a talent perspective, we collaborate with the Irish universities in research, but we’ve also had success identifying talent through student internships, collaborating and sponsoring PhDs - some of which are successful in applying for roles at CERENOVUS after completing their studies.”
At Janssen, interactive training has been customised and built in to ensure everyone keeps on track and up to date with digitalisation and sustainability. Gary Hartnett says: “We have found that we need different types of people too, such as data scientists.
“We’re partnering with universities because we want to build that diversity that can be found locally. People who have originally worked with large tech companies tend to like working in healthcare, they like the sense of purpose of it and importantly, we are retaining them.”
Transformation initiatives typically involve cross-functional collaboration and communication. Creating partnerships with university networks is an important way of finding and growing new talent. Michael Murphy at Boston Scientific says collaboration with universities is key. He says: “The company is working with universities in the West of Ireland to help increase the knowledge base and shape the courses that will generate the next wave of technical skills coming into the sector.”
Ireland’s collaborative networks between industries and partnerships and between industry and academia can provide the foundations needed to support companies through digitalisation. At Boston Scientific, strong partnerships have developed with data and technology companies to provide subsystems for its technologies.
IDA Ireland provides practical and financial support to companies undertaking innovation and transformation in their Irish based operations. IDA’s targeted transformation supports upskilling and talent development, innovation/R&D, digitalisation and sustainability. It is designed to help companies at all stages of their growth and transformation journey.
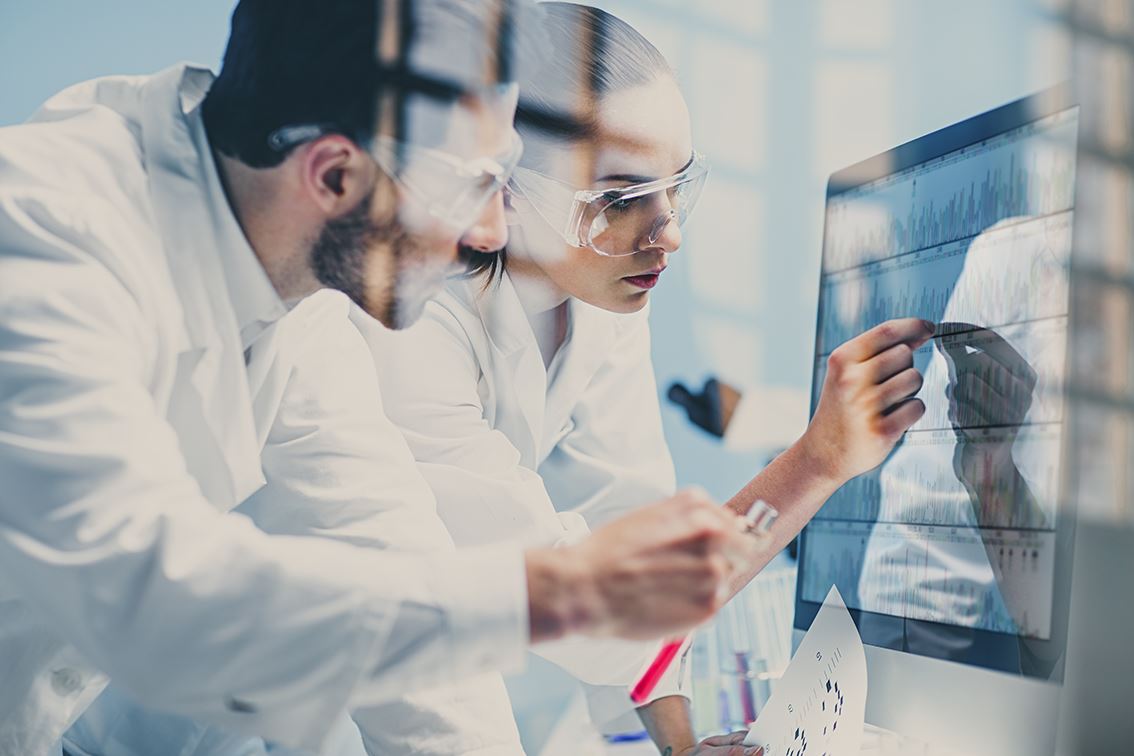
Conclusion
Rapid advances in MedTech underscore a global imperative for continuous innovation aimed at saving lives and enhancing the overall quality of life. Meeting the demands of this dynamic sector requires companies and innovators to not only keep pace with evolving patient needs but also to possess the flexibility and agility necessary to adapt to emerging global challenges. Ireland, as a globally recognised MedTech centre of excellence emerges as a strategic location, offering the essential stability, talent and ecosystem required to propel companies to the next level.Already global exemplars like WEF Lighthouses DePuy and Janssen, Ireland provides a conducive environment for MedTech companies seeking to bolster their digitalisation efforts, ensuring the future resilience of their operations. Beyond infrastructure and industry supports, Ireland facilitates collaboration with diverse educational institutions, suppliers and partners fostering an environment conducive to world class research and development.
Furthermore, the centralisation of commercial business services in Ireland is driving operational efficiencies and leveraging economies of scale by tapping into deep and diverse talent pools. The sophisticated workforce positions Ireland as an ideal destination for companies aspiring to thrive in the ever-evolving landscape of MedTech.
Additionally, Ireland's commitment to Climate Action emerges as a noteworthy priority. The country is actively supporting industry exemplars that showcase a dedication to sustainable practices. This aligns seamlessly with Government support for the dual transition towards digitalisation and sustainability, making Ireland not only a hub for innovation but also a model for responsible and sustainable investment in the MedTech sector.
In essence, Ireland stands as a shining example for MedTech advancement, offering an ecosystem that encompasses innovation, regulatory performance, talent and a commitment to sustainability and digital transformation. As the industry continues to transform, Ireland's role as a strategic partner to the MedTech industry is solidified, promising a landscape where companies can flourish, innovate responsibly, and contribute meaningfully to the wellbeing of individuals worldwide.